Optimizing Galvanizing Efficiency with Advanced Wiper Blocks
Optimizing Galvanizing Efficiency with Advanced Wiper Blocks
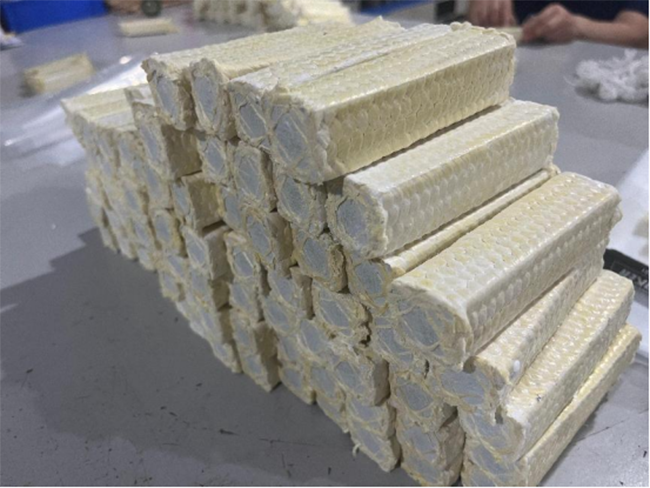
In the Galvanizing process, precise control of the zinc coating thickness is critical. Various wiper blocks on galvanizing lines ensure that excess zinc is efficiently removed, resulting in a uniform appearance.
The traditional oil charcoal wiper block uses charcoal mixed with oil to control the zinc layer through adsorption and mechanical wiping. However, it tends to agglomerate and generate oil smoke. An improved alternative is the water charcoal wiper block, which incorporates 20–30% water maintained by a spray system, reducing pollution and ensuring a cleaner steel surface.
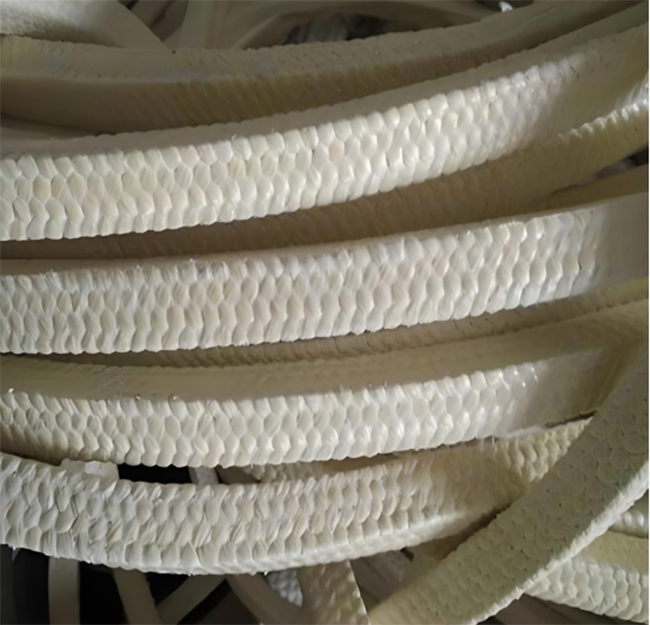
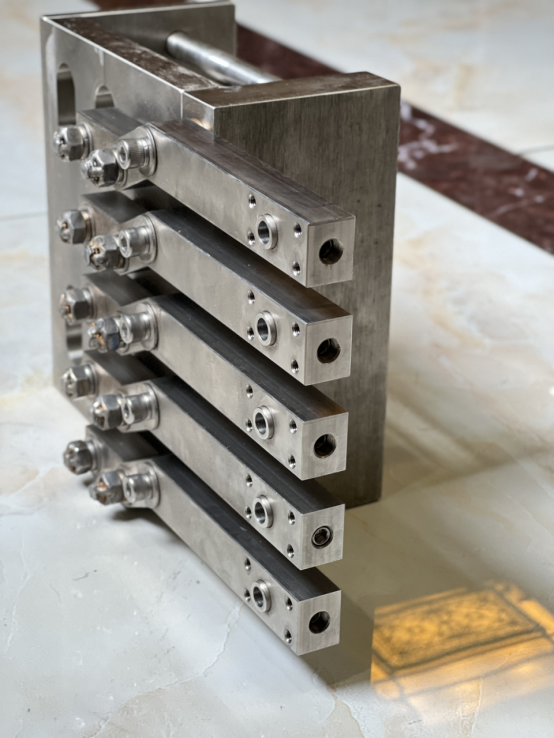
For enhanced heat resistance, the vermiculite wiping block leverages the porous mineral's adsorption capabilities. In contrast, the electromagnetic wiping technology utilizes alternating magnetic fields to induce Lorentz force, achieving contactless zinc removal. Meanwhile, the nitrogen wiping system employs high-pressure nitrogen injection for a residue-free finish, ideal for high-precision requirements.
Additional devices like industrial felt wipers and former asbestos clip modes have also been used. Each solution has unique advantages and is selected based on production line conditions, cost, and environmental requirements.
And now nitrogen wiping knife and wiping pad are very common to realize the galvanizing thickness which we can provide both. Thanks for reading!
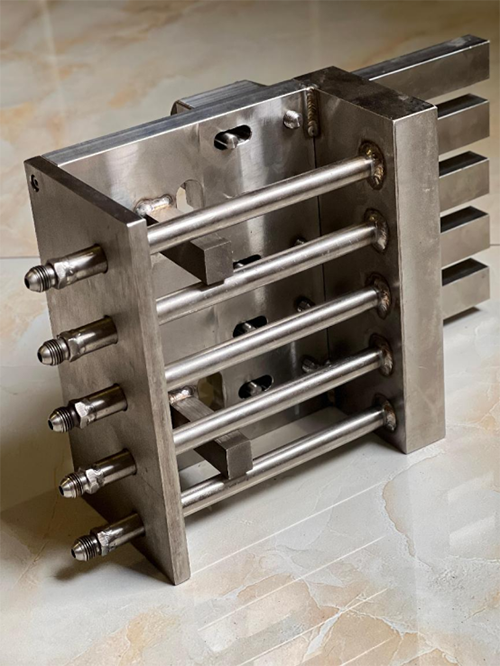